超声波焊接原理(二)
时间:2019-12-19 浏览:
1、超声波在塑料加工中的应用原理:
塑料加工中所用的超声波,现有的几种工作频率有15KHZ,18KHZ,20KHZ,40KHZ。其原理是利用纵波的波峰位传递振幅到塑料件的缝隙,在加压的情况下,使两个塑料件或其它件与塑料件接触部位的分子相互撞击产生融化,使接触位塑料熔合,达到加工目的。
强度的情况下,应尽可能去除。在有些情况下,先清洗塑料件是必要的。
碰到此种用小机台作大对象的情形,通常采取的方式有分好几次熔接、增加超音波输出功率(增加段)或增加熔接时间、压力等。然而这也产生了质量不稳定的现象,因为电压与气压直接影响到超音波输出功率的稳定性。
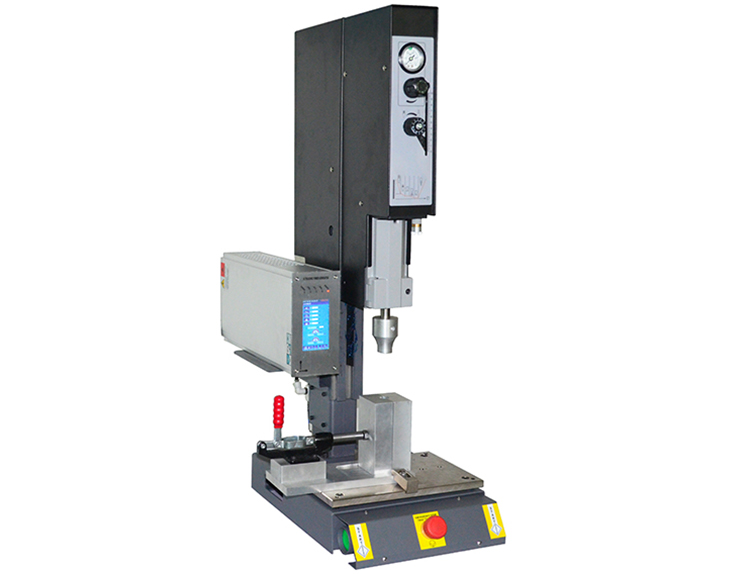
也就是说上班或尖峰时间,使用超音波作业的产品质量,与大家都下班后的质量稳定是不相同的。
然而大家都下了班再使用超音波,那就不是工作效率了。所以这时采取的对策就是气压源采取独立方式;要求在0.02m/m 以下之产品在超音波机台加装稳压设备;调整出力段数、增加功率,但一般状况超音波作业时功率输出最好能掌握在2~4 段之间,如一定要在5~6 段作业,则生产作业时间必须尽量缩短,以避免零件、振动子的损耗。增加能量扩大器(H o r n上模)的扩大。但扩大程度如果超出4:1,将对H o r n本身、音波、电流有极大的影响
焊接产品质量不稳定
最好的办法,选择大单位的超声波焊接设备,例如,我们欣宇超声波产品就很好的。质量无法稳定最主要因素是输出功率不能稳定,以导致无法形成稳定的摩擦热能。而如何让功率输出稳定?此乃决定于
机台输出功率;
〈2〉H o r N 扩大比;
〈3〉气压源;
〈4〉电压源等四项。
1、机台输出功率+H o r N扩大比率=实际可用功率。由此可知在一定产品实施超音波熔接时,于规划与设计的观点而言,机台输出功率愈强,相对H o r N的扩大比所设计的也愈小。
反之机台输出功率愈小,H o r N设计的扩大比也愈大。例如:2200W的超音波熔接机,H o r N的扩大比是2.5 倍。换成3200W超音波熔接机时,H o r N的扩大比可能只要1.5倍即可。然而并非强调超音波熔接机输出的功率要大,而是要对一项塑料产品实施超音波熔接时,给予最适合的环境作业,其间尚需考虑成本的预算,产品的功能需求,熔接标准等考虑再来规划出完整的工作设备与超音波使用技巧。
2、在了解上述各种影响超音波熔接质量的关键性原因后,工程师在设计时,首当熟悉并评估1. 产品质量要求功能标准;2.现有超音波设备; 超声波焊接机。
3. 决定产品设计的形态、技巧如超音波导熔线、产品定位、材质)。因为既然可用设备资源已经固定,那就必须用产品设计的技巧来配合现有可用的设备才是正确的。
4、在我们确定人为因素(1 ~ 2项)都无问题时,会发生质量不稳定现象,那肯定一个事实:即气压与电压产生的影响。在我们多年来处理质量不能稳定现象时,也同时发现,在工作时间内无法达到的质量标准,却在大家都下班,停止电压、气压多数同时使用时,意外的达到质量要求标准。因此也发现多人或多单位使用共同的气压与电压源时,由于空气压缩机通常我们会设定空气储存筒里面的气压低于2 ~ 4kg的情况时再自动打气充填这是一项形成的误差原因。而气压源经过管路到达熔接机时,由于熔接速度快,第一次超音波熔接的气压与第二次或第三次存留于管路的气压亦形成误差,如此将形成周期性或非周期性的质量异动。而电压也由于电力公司输出同时供数百万人都有机会同时使用,此时产生的电压降也不是我们所能控制,如此气压与电压的变量,确确实实的造成能量输出的变化,而影响精密质量的重要因素。当然必须列为诊断项目。
熔接后移位了
1.降低熔接压力。
2.底模加高,使其超过熔接线2m/m 以上。
3.使用超音波传导熔接。
4.上模(HRON)压到产品才发振。
5.修改塑料产品,增强定位。
产生伤痕断震裂烫伤
1.降低压力。
2.减少延迟时间(提早发振)。
3.减少熔接时间。
4.引用介质覆盖(如PE袋)。
5.模治具表面处理(硬化或镀铬)。
6.机台段数降低或减少上模扩大比。
7.易震裂或断之产品,治具宜制成缓冲,如软性树脂或覆盖软木塞等(此项指不影响熔接强度)。
8.易断裂产品于直角处加R角。
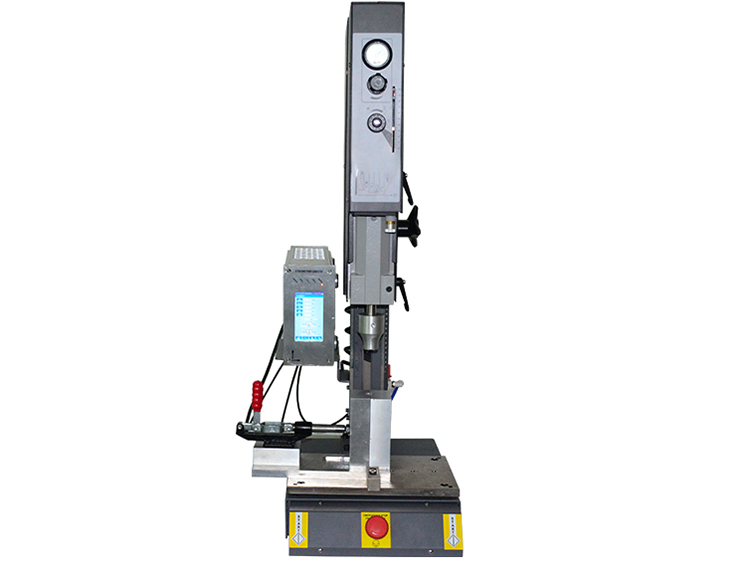
十六、超声波熔接后,发现变形扭曲怎么办?
1.降低压力(压力最好在2kg 以下)。
2.减少超音波熔接时间(降低强度标准)。
3.增加硬化时间(至少0.8 秒以上)。
4.分析超音波上下模是否可局部调整(非必要时)。
5.分析产品变形主因,予以改善。
熔接后内部零件破坏
1.提早超音波发振时间(避免接触发振)。
2.降低压力、减少超音波熔接时间(降低强度标准)。
3.减少机台功率段数或小功率机台。
4.降低超音波模具扩大比。
5.底模受力处垫缓冲橡胶。
6.底模与制品避免悬空或间隙。
7.H o r N(上模)逃孔后重测频率。
8.上模逃孔后贴上富弹性材料(如硅利康)。
超声波熔接后产品发现毛边或溢料
1.降低压力、减少超音波熔接时间(降低强度标准)。
2.减少机台功率段数或小功率机台。
3.降低超音波模具扩大比。
4.使用超音波机台微调定位固定。
5.修改超音波导熔线。 超声波机十九、超声波熔接后,发现产品尺寸不稳定怎么调?
1.增加熔接安全系数(依序由熔接时间、压力、功率)。
2.启用微调固定螺丝(应可控制到0.02m/m)。
3.检查超音波上模输出能量是否足够(不足时增加段数)。
4.检查治具定位与产品承受力是否稳合。
5.修改超音波导熔线。
产品总是单边烫伤
超音波振动熔接,并非单纯直线纵向振动(挠曲与横向振动不在此本次讨论中),而是形成交叉式纵向下降振动,而上模超音波输出端能量亦是有一定的强弱分布点,气压、电压、机台虽决定功率输出能量的稳定性,但能量分布点亦呈现比例性增减。
如果发现超音波熔接时制品总是单点烫伤,即表示上模该点输出能量与产品该点形成应力对应,此时若改变超音波振动面的接触点,将可改善热能集束产生的烫伤。
超声波焊接是熔接热塑性塑料制品的高科技技术,各种热塑性胶件均可使用超声波焊接处理,而不需加溶剂,粘接剂或其他辅助品,其优点是增加多倍生产率,降低成本,提高产品质量。
超声波塑胶焊接原理:由发生器产生20KHZ,(或15KHZ)的高压,高频信号,通过换能系统,把信号转换为高频机械振动,加于塑料制品工件上,通过工作表面及内在分子间的磨擦而使传导到接口的温度升高,当温度达到此工件本身的熔点时,使工件焊接口迅速溶化,继而填充于接口间的空隙,当振动停止,工件同时在一定的压力下冷却定型,便达成完美的焊接。
一通电就有超声波焊接的声音
分析原因:
1.开机后电流表动
2.开机后电流表不动解决方法:
1.检测主板是否损坏,维修主板
2.没多大问题,可能受到干扰超声波熔接后产生伤痕
塑料加工中所用的超声波,现有的几种工作频率有15KHZ,18KHZ,20KHZ,40KHZ。其原理是利用纵波的波峰位传递振幅到塑料件的缝隙,在加压的情况下,使两个塑料件或其它件与塑料件接触部位的分子相互撞击产生融化,使接触位塑料熔合,达到加工目的。
强度的情况下,应尽可能去除。在有些情况下,先清洗塑料件是必要的。
碰到此种用小机台作大对象的情形,通常采取的方式有分好几次熔接、增加超音波输出功率(增加段)或增加熔接时间、压力等。然而这也产生了质量不稳定的现象,因为电压与气压直接影响到超音波输出功率的稳定性。
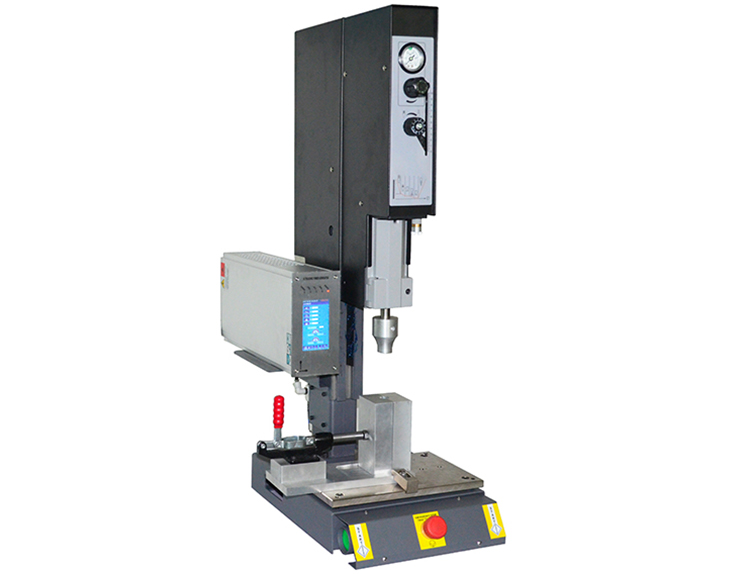
也就是说上班或尖峰时间,使用超音波作业的产品质量,与大家都下班后的质量稳定是不相同的。
然而大家都下了班再使用超音波,那就不是工作效率了。所以这时采取的对策就是气压源采取独立方式;要求在0.02m/m 以下之产品在超音波机台加装稳压设备;调整出力段数、增加功率,但一般状况超音波作业时功率输出最好能掌握在2~4 段之间,如一定要在5~6 段作业,则生产作业时间必须尽量缩短,以避免零件、振动子的损耗。增加能量扩大器(H o r n上模)的扩大。但扩大程度如果超出4:1,将对H o r n本身、音波、电流有极大的影响
焊接产品质量不稳定
最好的办法,选择大单位的超声波焊接设备,例如,我们欣宇超声波产品就很好的。质量无法稳定最主要因素是输出功率不能稳定,以导致无法形成稳定的摩擦热能。而如何让功率输出稳定?此乃决定于
机台输出功率;
〈2〉H o r N 扩大比;
〈3〉气压源;
〈4〉电压源等四项。
1、机台输出功率+H o r N扩大比率=实际可用功率。由此可知在一定产品实施超音波熔接时,于规划与设计的观点而言,机台输出功率愈强,相对H o r N的扩大比所设计的也愈小。
反之机台输出功率愈小,H o r N设计的扩大比也愈大。例如:2200W的超音波熔接机,H o r N的扩大比是2.5 倍。换成3200W超音波熔接机时,H o r N的扩大比可能只要1.5倍即可。然而并非强调超音波熔接机输出的功率要大,而是要对一项塑料产品实施超音波熔接时,给予最适合的环境作业,其间尚需考虑成本的预算,产品的功能需求,熔接标准等考虑再来规划出完整的工作设备与超音波使用技巧。
2、在了解上述各种影响超音波熔接质量的关键性原因后,工程师在设计时,首当熟悉并评估1. 产品质量要求功能标准;2.现有超音波设备; 超声波焊接机。
3. 决定产品设计的形态、技巧如超音波导熔线、产品定位、材质)。因为既然可用设备资源已经固定,那就必须用产品设计的技巧来配合现有可用的设备才是正确的。
4、在我们确定人为因素(1 ~ 2项)都无问题时,会发生质量不稳定现象,那肯定一个事实:即气压与电压产生的影响。在我们多年来处理质量不能稳定现象时,也同时发现,在工作时间内无法达到的质量标准,却在大家都下班,停止电压、气压多数同时使用时,意外的达到质量要求标准。因此也发现多人或多单位使用共同的气压与电压源时,由于空气压缩机通常我们会设定空气储存筒里面的气压低于2 ~ 4kg的情况时再自动打气充填这是一项形成的误差原因。而气压源经过管路到达熔接机时,由于熔接速度快,第一次超音波熔接的气压与第二次或第三次存留于管路的气压亦形成误差,如此将形成周期性或非周期性的质量异动。而电压也由于电力公司输出同时供数百万人都有机会同时使用,此时产生的电压降也不是我们所能控制,如此气压与电压的变量,确确实实的造成能量输出的变化,而影响精密质量的重要因素。当然必须列为诊断项目。
熔接后移位了
1.降低熔接压力。
2.底模加高,使其超过熔接线2m/m 以上。
3.使用超音波传导熔接。
4.上模(HRON)压到产品才发振。
5.修改塑料产品,增强定位。
产生伤痕断震裂烫伤
1.降低压力。
2.减少延迟时间(提早发振)。
3.减少熔接时间。
4.引用介质覆盖(如PE袋)。
5.模治具表面处理(硬化或镀铬)。
6.机台段数降低或减少上模扩大比。
7.易震裂或断之产品,治具宜制成缓冲,如软性树脂或覆盖软木塞等(此项指不影响熔接强度)。
8.易断裂产品于直角处加R角。
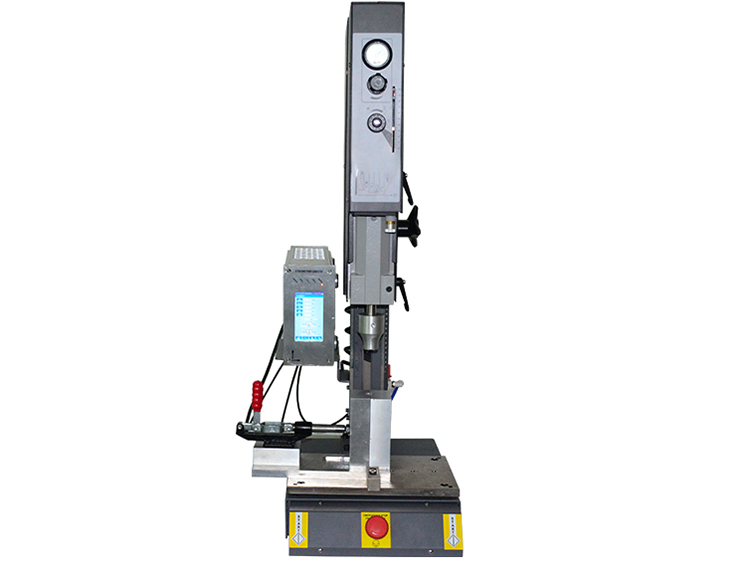
十六、超声波熔接后,发现变形扭曲怎么办?
1.降低压力(压力最好在2kg 以下)。
2.减少超音波熔接时间(降低强度标准)。
3.增加硬化时间(至少0.8 秒以上)。
4.分析超音波上下模是否可局部调整(非必要时)。
5.分析产品变形主因,予以改善。
熔接后内部零件破坏
1.提早超音波发振时间(避免接触发振)。
2.降低压力、减少超音波熔接时间(降低强度标准)。
3.减少机台功率段数或小功率机台。
4.降低超音波模具扩大比。
5.底模受力处垫缓冲橡胶。
6.底模与制品避免悬空或间隙。
7.H o r N(上模)逃孔后重测频率。
8.上模逃孔后贴上富弹性材料(如硅利康)。
超声波熔接后产品发现毛边或溢料
1.降低压力、减少超音波熔接时间(降低强度标准)。
2.减少机台功率段数或小功率机台。
3.降低超音波模具扩大比。
4.使用超音波机台微调定位固定。
5.修改超音波导熔线。 超声波机十九、超声波熔接后,发现产品尺寸不稳定怎么调?
1.增加熔接安全系数(依序由熔接时间、压力、功率)。
2.启用微调固定螺丝(应可控制到0.02m/m)。
3.检查超音波上模输出能量是否足够(不足时增加段数)。
4.检查治具定位与产品承受力是否稳合。
5.修改超音波导熔线。
产品总是单边烫伤
超音波振动熔接,并非单纯直线纵向振动(挠曲与横向振动不在此本次讨论中),而是形成交叉式纵向下降振动,而上模超音波输出端能量亦是有一定的强弱分布点,气压、电压、机台虽决定功率输出能量的稳定性,但能量分布点亦呈现比例性增减。
如果发现超音波熔接时制品总是单点烫伤,即表示上模该点输出能量与产品该点形成应力对应,此时若改变超音波振动面的接触点,将可改善热能集束产生的烫伤。
超声波焊接是熔接热塑性塑料制品的高科技技术,各种热塑性胶件均可使用超声波焊接处理,而不需加溶剂,粘接剂或其他辅助品,其优点是增加多倍生产率,降低成本,提高产品质量。
超声波塑胶焊接原理:由发生器产生20KHZ,(或15KHZ)的高压,高频信号,通过换能系统,把信号转换为高频机械振动,加于塑料制品工件上,通过工作表面及内在分子间的磨擦而使传导到接口的温度升高,当温度达到此工件本身的熔点时,使工件焊接口迅速溶化,继而填充于接口间的空隙,当振动停止,工件同时在一定的压力下冷却定型,便达成完美的焊接。
一通电就有超声波焊接的声音
分析原因:
1.开机后电流表动
2.开机后电流表不动解决方法:
1.检测主板是否损坏,维修主板
2.没多大问题,可能受到干扰超声波熔接后产生伤痕